AGVs and AMRs: Optimizing Workflow and Driving Innovation
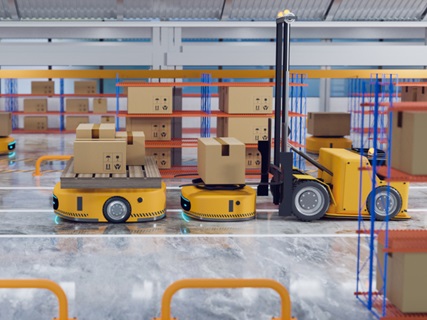
Autonomous guided vehicles (AGVs) and autonomous mobile robots (AMRs) have rapidly become indispensable to modern manufacturing and logistics. By navigating factory floors and warehouses with little to no human intervention, these robotic systems streamline material flow, enhance safety, and boost overall operational efficiency.
Why AGVs and AMRs Are Gaining Ground
The rising adoption of AGVs and AMRs is due to advancements in sensing, control algorithms, and computing power. Traditional manual handling and transport methods can be labor-intensive and error-prone, especially when dealing with high-throughput environments. By contrast, AGVs and AMRs typically move materials, products, or components with speed and precision, allowing human workers to focus on higher-value tasks. Over time, the cost-effectiveness and scalability of these systems have enabled their proliferation across various industries.
Key Sectors Benefiting from AGVs and AMRs:
- Manufacturing: AGVs and AMRs transport raw materials and finished parts between workstations, helping manufacturers meet production targets and reduce factory floor congestion.
- Logistics and Warehousing: By automating the storage and retrieval of goods, AGVs and AMRs support faster order fulfillment and more accurate inventory management. They navigate busy warehouse environments safely, mitigating risks of collisions and enabling 24/7 operations.
- Automotive: These robots ferry large components (like chassis or engines) along assembly lines, minimizing downtime and improving workflow synchronization.
- eCommerce: AMRs excel at picking operations, quickly bringing shelves or individual items to human operators, accelerating order processing and improving accuracy.
Core Technologies Powering AGVs and AMRs
- Navigation and Mapping: Advanced sensors—such as lidar, cameras, and inertial measurement units—enable localization, obstacle detection, and path planning. These features allow AGVs and AMRs to traverse dynamic environments with minimal errors.
- Control Systems and Algorithms: Robust control algorithms help maintain stability, manage speed, and handle real-time decision-making. Modules for collision avoidance and route optimization are critical for ensuring smooth operations.
- Connectivity and Data Sharing: AGVs and AMRs often connect to warehouse management systems or higher-level supervisory controls via wireless protocols. This connectivity helps coordinate multiple robots, optimize routes, and provide real-time performance monitoring.
- Energy Efficiency: Innovations in battery technologies and motor drivers extend the runtime of mobile robots, allowing them to complete more tasks between charges or battery swaps.
Subsystems in AGVs and AMRs
- Lift and Wheel Control: The lift and wheel control subsystem manages vertical movements and directional steering. It ensures precise motor operation for raising heavy loads, controlling wheel torque, and coordinating navigation algorithms for smooth, efficient movement across dynamic industrial floors.
- Battery Monitoring: Batteries power AGVs/AMRs, requiring robust monitoring to track charge levels, health, and usage trends. Intelligent battery management determines when to recharge or swap batteries, enhancing productivity by minimizing unexpected downtime and ensuring consistent operation throughout demanding shifts.
- Obstacle Detection: Obstacle detection systems combine sensors—like lidar, ultrasonic, or camera arrays—to identify people, equipment, and other potential hazards. Accurate detection and responsive software logic help AGVs/AMRs avoid collisions, maintain safe speeds, and adapt to changing floor conditions in real time.
Challenges and Considerations for AGVs and AMRs
- Scalability: As operations expand, integrating more robots without network congestion or collisions becomes complex.
- Adaptability: Dynamic environments require flexible robots capable of making quick navigation decisions when unexpected changes arise, such as personnel presence or blocked pathways.
- Security: Connected robots are vulnerable to cybersecurity threats, requiring robust encryption and authentication measures.
- Safety: With robots operating alongside human workers, ensuring collision avoidance and adherence to strict safety standards is essential.
Innovation and Future Outlook
Ongoing research and development in sensing, artificial intelligence, and collaborative robotics are opening the door to even more sophisticated AGVs and AMRs. For instance, robots that leverage machine learning for predictive maintenance can identify when part failures are likely to occur, minimizing unplanned downtime. As technology continues to advance, the possibility of larger-scale autonomous systems working collaboratively grows closer to reality.
Conclusion
AGVs and AMRs play a pivotal role in streamlining intralogistics, reducing operational costs, and enhancing worker safety in manufacturing and warehousing. With demand for these autonomous vehicles steadily increasing, there is a pressing need for efficient, reliable, and scalable solutions. Allegro Microsystems empowers the development of high-performance AGVs and AMRs, providing robust current sensors, position sensors, and motor drivers to help engineers address modern automation challenges. Visit Allegro’s AGV/AMR Robotics page to learn how Allegro can support your next-generation AGV or AMR design.