Cobots: Revolutionizing Manufacturing Through Human-Robot Collaboration
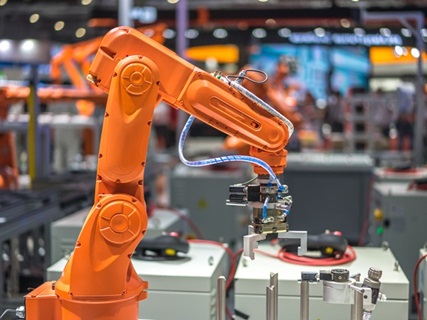
Collaborative robots (cobots) are fundamentally changing the landscape of industrial automation. Unlike traditional industrial robots that operate in isolation behind safety barriers, cobots are designed to work safely alongside human operators, combining the precision and consistency of automation with human intelligence and adaptability. This revolutionary approach is opening new possibilities in manufacturing, assembly, and quality control across diverse industries.
Why Cobots Are Gaining Momentum
The rise of cobots is driven by several key factors that address modern manufacturing challenges. Traditional automation often requires significant infrastructure investment and dedicated workspace, making it impractical for many applications. Cobots, by contrast, can be easily integrated into existing workflows without extensive facility modifications. The flexibility of cobots makes them particularly valuable in today's dynamic manufacturing environment. They can be quickly reprogrammed for different tasks, making them ideal for small-batch production and customized manufacturing. This adaptability, combined with their ability to work safely near humans, has made cobots an attractive solution for manufacturers seeking to enhance productivity without completely overhauling their operations.
Key Sectors Benefiting from Cobots:
- Manufacturing and Assembly: Cobots excel in precision assembly tasks, working alongside human operators to handle delicate components or perform repetitive operations with micron-level accuracy.
- Automotive Industry: From engine assembly to quality inspection, cobots streamline automotive production by handling heavy components while maintaining flexibility to adapt to different vehicle models.
- Healthcare and Pharmaceuticals: Cobots ensure consistent quality in drug packaging and laboratory automation while maintaining strict hygiene and safety standards.
- Food and Beverage: Used in food processing and packaging, cobots maintain hygiene standards while assisting with food preparation and quality control.
Core Technologies Powering Cobot Systems:
- Advanced Control Architecture: Distributed control with main processors handling trajectory planning and individual joint controllers managing local motor control for faster response times.
- Power Management: 48V architecture with multi-voltage distribution (48V for motors, 12V for control) requiring sophisticated DC/DC conversion and thermal management.
- Precision Sensing: Magnetic current sensors for motor control and safety monitoring; absolute position sensors for precise joint positioning and collision detection.
Subsystems in Cobot Design:
- Power Supply: The power supply subsystem provides regulated power distribution throughout the cobot system. Modern cobots typically use 48V main power rails for improved efficiency and higher payload capabilities, with additional regulated voltages for control electronics. The power architecture must handle varying loads as joints move and provide clean, stable power for sensitive control circuits. Efficient DC/DC converters are essential for managing power distribution while minimizing heat generation in the compact joint assemblies.
- Servo Motor Controller: The servo motor controller subsystem manages precise motor control for each joint, combining motor drivers, current sensing, and position feedback. Advanced magnetic current sensors enable accurate torque control and provide safety monitoring for collision detection. High-resolution position sensors support smooth motor commutation and precise joint positioning. The controller must balance high-performance motor control with the safety requirements necessary for human collaboration, including real-time monitoring and fault protection.
- Robot Joints: The robot joints subsystem integrates mechanical components with electronic control to create the 6-degree-of-freedom motion capability. Each joint contains motors, gearboxes, sensors, brake systems, and local control electronics in a compact assembly. Joint brake systems provide safety through electromagnetic or solenoid-based mechanisms that can safely stop motion in emergency situations. The mechanical design must accommodate all electronic components while maintaining the precision and reliability required for collaborative operation.
Challenges and Considerations for Cobot Development:
- Balancing Performance and Safety: One of the primary challenges is achieving high performance while maintaining safety characteristics necessary for human collaboration. This requires careful optimization of control algorithms, sensor systems, and mechanical design.
- Cost and Complexity Management: While cobots are generally more affordable than traditional industrial robots, managing system costs while delivering required performance remains challenging. This drives the need for highly integrated solutions that reduce component count without compromising functionality.
- Scalability and Standardization: As cobot adoption grows, manufacturers seek standardized approaches including communication protocols, modular hardware designs, and common software frameworks to reduce development time and cost.
Innovation and Future Outlook
The future of cobot technology is being shaped by advances in artificial intelligence, sensor technology, and human-machine interfaces. Machine learning algorithms enable more sophisticated collision avoidance and adaptive behavior, while advanced sensors provide richer environmental awareness. Force and torque sensing capabilities are becoming more sophisticated, enabling delicate assembly tasks requiring precise force control. Vision systems are also becoming more integrated, allowing cobots to adapt to variations in part positioning and quality.
Conclusion
Cobots represent a fundamental shift in industrial automation, offering the potential to combine human creativity with robotic precision. As the technology matures, cobots will play an increasingly important role in manufacturing across diverse industries. The success of cobot implementations depends heavily on underlying electronic systems that enable precise control, reliable operation, and safe human interaction. As cobots become more capable and affordable, they will likely expand beyond traditional manufacturing into healthcare, logistics, and service industries, fundamentally changing human-robot collaboration in the workplace.