Modern Motor Drivers Enable a Common Platform for Power Tool Designs
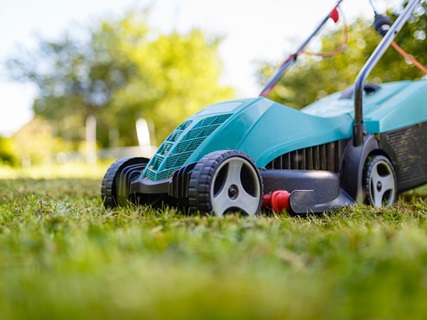
In today’s diverse power tool market, the wide range of battery voltages and torque requirements often result in designs that use different platforms that support a limited range of products. Significant time and cost could be cut from research and development schedules if a single industry-wide platform were used to serve the range of planned products.
Some power tool lineups span the 12 V to 24 V range, while others span the 12 V to 60 V range. If you include lawn tools, the range can extend to 80 V. With these higher operational battery voltages come harsher environments that introduce larger negative transients on the driver output stages, necessitating multiple printed circuit board (PCB) designs that draw from a grab bag of low- and high-power motor driver chips. A common brushless DC (BLDC) or half-bridge driver chip that spans the entire range of power tool designs available in the market would reduce the time and effort required to develop and produce new power tools, consolidating software development time and PCB design/test cycles.
A single platform design that can serve the full range of power tools in the market must allow for the full range of maximum voltages across those devices. Many motor driver devices have a maximum supply voltage of only 40 V. This does not leave adequate margin in most 24 V or 36 V systems to deliver a robust design that can withstand the harsh voltage transients that may arise on the power-tool voltage supply during motor operation. A standalone gate driver with a broader supply voltage range that can withstand these transients—such as the 50 V and higher gate drivers discussed below—would allow system designers to achieve the time and resource savings of a common design across a large span of power-tool batteries.
For higher-power 48 V, 60 V, or 80 V systems, fewer solutions exist for the integrated three-phase BLDCs. The necessary power tool design may be easier to achieve when power is distributed around the board with compact high-voltage half bridges. A 100 V half bridge in an ultra-small 3 mm × 3 mm DFN package w
ould help toward this goal. The wide supply voltage range allows for use in small 12 V drill motors or more-powerful 80 V string trimmers with a single PCB architecture, where—to save cost for low-power tools—various MOSFETS can be swapped in and out according to the power level needed.
High-end power tools often support extended operation times or operation with frequent, rapid, high-power bursts. They may also have peak torque ratings in excess of 1200 in-lb or 130 N∙m, commonly calculated at 2000 rpm. On the other end of the spectrum, battery-powered lawn mowers require less torque, yet still demand high-speed operation for long durations. This dictates that the gate driver for a common platform needs to be able to drive both a 12 V, 30 kW peak power drill and an 80 V, 4.5 kW lawn mower. When the common torque ratings of two tools are converted into power, the span that a driver needs to accommodate is shown by:
Power [kW] = (Torque [N∙m] × Speed [rpm])/9550
High-power drill peak example:
Power = (130 N∙m × 2100 rpm)/9550 = 27.6 kW
Low-power long-duration lawn mower example:
Power = (12 N∙m × 3500 rpm)/9550 = 4.4 kW
The above power levels determine what driver and MOSFET to use in any given system.
Most drivers have gate drive voltages in the range of 7 V to 13 V. The total gate charge varies significantly for some of the MOSFETs commonly used in these devices at a nominal 10 V. A low-profile 40 V DFN MOSFET may have a total gate charge of 65 nC, while a 100 V MOSFET may have a total gate charge of only 35 nC. To ensure support for the full power spectrum of the tool lineup, consideration must be made for the average VREG current that the driver can supply to the gate of the MOSFET to hold the MOSFET in the on state.
Consideration must also be made for the maximum source and sink currents to ensure that the MOSFET advances quickly through the Miller region; however, the limiting factor of the pulse-width-modulated (PWM) drive frequency and MOSFET size will be the average current the driver can supply the gate drive. The equation to determine the necessary average VREG drive current needed to hold the MOSFETs in the on state at a given PWM frequency is:
Iavg [mA] = Number of MOSFETs being driven × fPWM [kHz] × QG(tot) [nC] × 1000
For example:
I(100V_FET,AVG) = 6 × 20 kHz × 35 nC × 1000 = 4.2 mA
I(40V_FET,AVG) = 6 × 20 kHz × 65 nC × 1000 = 8 mA
I(80V_FET,AVG) = 6 × 20 kHz × 140 nC × 1000 = 17 mA
The number of MOSFETs being driven changes with the driver scheme–six are used for sinusoidal drivers, two are used for trapezoidal drivers, and four are used for two-phase sinusoidal drivers. In the examples, 20 kHz is used to keep the drive frequency out of the audible range.
Figure 1: Graph of common driver IREG capabilities and calculation of current needed to maintain the on state for six 35 nC MOSFETs at various PWM frequencies.
Many more MOSFET options exist and the values for total gate charges are infinite. The key point is that, in any system, the designer must address the interplay of components that affect the average VREG driver current before the driver is selected. Using a MOSFET with a 65 nC total gate charge at 10 V, a driver with an IREG average current of 15 mA driven at 20 kHz would provide plenty of margin for a strong gate drive. Using the same design for a lower-power tool, the MOSFET could be swapped with a lower ID-rated device with higher total gate charge.
Figure 2: Capable motor drivers allow for flexible PCB designs.
Systems that span the 12 V to 80 V range require a driver with a higher supply rating that supports the high-power 18 V drill and the 80 V mower. Although the choice of suitable integrated three-phase BLDC drivers is limited, a set of capable 100 V half bridges may meet the need. The Allegro A89500 [1] is a 100 V-rated half bridge that can drive a 30 kW or 4 kW system. The peak sink and source currents are high enough to quickly switch the MOSFETs to the on state and can be easily set with external resistors for a highly flexible and robust electromagnetic-compatible (EMC) design. The separate gate drive supply then supports all the current needed to keep the MOSFETs in the on state during high-current 100% duty cycle situations.
Figure 3: Systems that span the 12 V to 80 V range require a driver with a higher supply rating that supports the high-power 18 V drill and the 80 V mower.
The next consideration in the design of a power tool system is the robustness of the driver. How will it perform in harsh environments with large transients generated by high-torque motors?
When a driver switches the MOSFETs that control a motor with a peak power rating of 30 kW, large positive and negative transient pulses are bound to occur. A system designer can either place numerous capacitors on the MOSFET bridge supply or choose a driver that has best-in-class transient protection and save PCB space and BOM cost. The Allegro portfolio of power tool gate drivers—like the 50 V-rated A4919 [2] and the 100 V-rated A89500—offer best-in-class negative transient protection built directly into the circuitry. The high-side gate driver output of the A89500 can withstand voltages on the phase connections of short-duration transients at –18 V up to 100 V. The A4919 and the A4915 [3] (a similarly sized device for sub-40 V tools) are popular options for power tools, delivering best-in-class negative transient robustness on the phase connections as well. Although a few other choices for this market are robust to –8 V at the phase connection, many vendors can only support ~2 V below ground. These less-robust solutions would require separate PCB designs for the harsher high-power tools or significant protection circuitry that would be otherwise unneeded on the low-power end of the power tool market.
Figure 4: Phase connection transient robustness and maximum supply voltage rating of Allegro and other vendor gate drivers.
To determine the best driver for a design that supports a range of tools, the system integrator must consider several questions. What is the battery voltage range among all the tools in the lineup? What size MOSFETs will be needed? Will there be room for extra protection circuitry, or can it be brought into the gate driver?
Whatever the system, devices are currently available that can enable a common platform for power tool designs. The A4919 is a small direct-drive gate driver with robust gate drive circuitry capable of supporting most systems below 40 V. The A4915 is a similarly sized device for sub-40 V tools and features an integrated Hall-effect sensor supply and feedback along with the motor drive control logic. The A4915’s built-in control logic saves space with a simple interface that offloads motor-control algorithms. For tool portfolios that span the range from 12 V to 80 V, the small and capable A89500 half bridge is the best choice, easily driving high-power MOSFETs with high total gate charges or small, multipack low-power MOSFETs. All of these devices allow system designers to condense a power tool lineup to a single PCB, which saves test time, offloads software resources, and enables faster development.
Based on the article “Modern Motor Drivers Enable a Common Platform for Power Tool Designs,” by Charles Keefer, originally published in All About Circuits, March 31, 2022. Republished with permission. For portions not copyrighted by original publisher, Copyright ©2022, Allegro MicroSystems, Inc.