Magnetic Position Sensors in Robotics
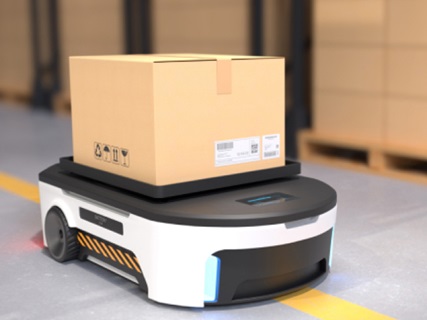
A key function of any robot is to interact with the physical world surrounding it. To achieve this, robots contain various actuators that require accurate position sensing to enable precise movement and functionality. From simple head-on proximity detection to measuring the absolute position of linear or rotational travel, magnetic position sensors offer high accuracy, contactless proprioceptive sensor solutions to support system precision and reliability. Figure 1 shows an example of the physical setup of the sensing orientations. In this article, the various types of magnetic position sensors, their benefits, and their applications in robotics will be discussed.
Figure 1: Magnetic Sensing orientations Left: head-on, Center: Slide-By, Right: Angle
Hall-effect switches are one of the simplest but most important magnetic sensors. These sensors act as a comparator with thresholds set to define the presence or absence of a magnet; they are commonly used for limit switch or open/close detection applications. Hall-effect switches can replace mechanical switches, such as reed and micro switches, and offer a solid-state sensing solution. Over time, mechanical switches with moving parts will wear out, resulting in degradation of switching consistency and requiring premature repairs or replacements. In addition to reliability, Hall switches have stable performance across temperature and are offered in low-power options to support applications where passive components were previously used. Hall-effect switches can be used in robotic applications to ensure proper docking into charging stations, to notify of openings or potential tampering, and to act as a limit switch for end of travel or range detection. For more information on the technical considerations necessary to aid with the replacement of a mechanical switch with a Hall-effect switch, see “Introduction to Hall-Effect Switches and Conversion from Mechanical Switches” application note available on the Allegro website.
Hall-effect latches are like Hall-effect switches but require alternating north and south magnetic poles to toggle the sensor output, which is why they are primarily used in motors or rotating applications. Magnetic latches are commonly used in brushless DC (BLDC) motors for commutation or in brushed DC motors for speed and, if desired, direction sensing. Hall-effect latches come in 1D or 2D options. The 2D option combines two latch outputs into a single-chip solution and offers flexibility in the sensor and magnet placement or enables a quadrature output for position encoding. These low cost and easy to integrate solutions can work for a variety of motors within a robotic system. For example, in robotic vacuum cleaners, 2D latches can be used in wheel motors as encoders for navigation odometry. 1D latches can be integrated for commutation signals in the suction pump for vacuuming, or even speed detection for brushed DC motors.
Absolute magnetic position sensors come in many different forms and technologies. The simplest is the 1D linear Hall sensor, which can be used to track the position of slide-by or head-on travel along a single-axis and provides a powerful solution when used in an array of multiple sensors for longer distances. A 3D sensor offers precise position feedback in multiple directions. With the advancing capabilities of transport systems for material handling in factory automation, 1D and 3D linear Hall-effect sensors are highly suitable solutions to determine the location of multiple internal mechanisms moving at different speeds and positions.
3D sensors can also be used in rotary applications and complex 3D motion such as joysticks. In certain configurations, an angle can be calculated from two outputs of the 3D sensor. This is good for low-speed applications. However, the 2D angle sensors are optimized for precision in high-speed motor position sensing.
2D angle position sensors provide low-latency angle outputs that enable smoother and more efficient motor control. Due to the increasing need for accurate position and speed control, servo motors are rapidly growing in industrial automation. Although high-resolution encoders have primarily used optical solutions for feedback, magnetic solutions are continuously evolving to achieve higher levels of accuracy and offer some key benefits over their mechanical counterpart, including lower current consumption, smaller size with flexible end-of-shaft or side-shaft sensing, and the ability to withstand contaminants and harsh conditions.
Allegro is constantly developing new and innovative solutions to provide its customers with the best solutions. For magnetic position sensing, the Tunneling Magneto Resistance (TMR) parts incorporate a new transducer that introduces the next generation of accuracy, precision, and power savings performance in our devices. These TMR-based sensors can be used in the same applications as their hall-based counterparts. However, the increased performance comes with an increased cost.
Allegro offers a broad selection, encompassing a wide range of performance and cost targets, for each type of magnetic position sensor discussed previously. Table 1 The continuously growing robotic market and its need for higher performance and system reliability go together with Allegro’s cutting-edge technology to offer industry-leading accuracy and safety.
Table 1: Recommended Parts
Category |
Use Cases |
Allegro Product |
Additional Detail |
Hall-Effect Switch |
On/off, open/close, limit switch |
High voltage |
|
Micropower |
|||
TMR |
|||
Micropower 3D switch |
|||
Hall-Effect Latch |
Commutation |
High voltage |
|
High voltage, Safety ready |
|||
2D Speed/direction |
Flexible, one-chip solution |
||
1D Linear Position Sensor |
Linear torque sensor |
Low noise |
|
Slide-by, end of travel |
External reference and enable pin |
||
TMR |
|||
Angle |
Low noise |
||
3D Magnetic Position Sensor |
Encoder feedback – linear and rotary |
Single die SOIC-8, Dual die TSSOP-14 |
|
3-pin PCB-less SIP package |
|||
2D Angle Position Sensor |
Motor control or rotary encoder feedback |
SPI, SENT, or PWM output |
|
Stray field immune |
|||
SIN/COS output |
|||
TMR SIN/COS output |